Teknologi pemotongan wafer, sebagai langkah penting dalam proses produksi semikonduktor, secara langsung terkait dengan kinerja chip, hasil, dan biaya produksi.
#01 Latar Belakang dan Arti Wafer Dicing
1.1 Definisi Wafer Dicing
Pemotongan wafer (juga dikenal sebagai scribing) merupakan langkah penting dalam manufaktur semikonduktor, yang bertujuan untuk membagi wafer yang telah diproses menjadi beberapa cetakan individual. Cetakan ini biasanya berisi fungsionalitas sirkuit lengkap dan merupakan komponen inti yang pada akhirnya digunakan dalam produksi perangkat elektronik. Seiring dengan semakin kompleksnya desain chip dan semakin kecilnya dimensi, persyaratan presisi dan efisiensi untuk teknologi pemotongan wafer menjadi semakin ketat.
Dalam praktiknya, pemotongan wafer biasanya menggunakan alat presisi tinggi seperti pisau berlian untuk memastikan setiap cetakan tetap utuh dan berfungsi penuh. Langkah-langkah kunci meliputi persiapan sebelum pemotongan, kontrol presisi selama proses pemotongan, dan pemeriksaan kualitas setelah pemotongan.
Sebelum pemotongan, wafer harus ditandai dan diposisikan untuk memastikan jalur pemotongan yang akurat. Selama pemotongan, parameter seperti tekanan dan kecepatan pahat harus dikontrol secara ketat untuk mencegah kerusakan pada wafer. Setelah pemotongan, inspeksi kualitas menyeluruh dilakukan untuk memastikan setiap keping memenuhi standar kinerja.
Prinsip dasar teknologi pemotongan wafer tidak hanya mencakup pemilihan peralatan pemotong dan pengaturan parameter proses, tetapi juga pengaruh sifat mekanik dan karakteristik material terhadap kualitas pemotongan. Misalnya, wafer silikon dielektrik low-k, karena sifat mekaniknya yang rendah, sangat rentan terhadap konsentrasi tegangan selama pemotongan, yang menyebabkan kegagalan seperti terkelupas dan retak. Kekerasan dan kerapuhan material low-k yang rendah membuatnya lebih rentan terhadap kerusakan struktural akibat gaya mekanis atau tekanan termal, terutama selama pemotongan. Kontak antara alat dan permukaan wafer, ditambah dengan suhu tinggi, dapat semakin memperparah konsentrasi tegangan.
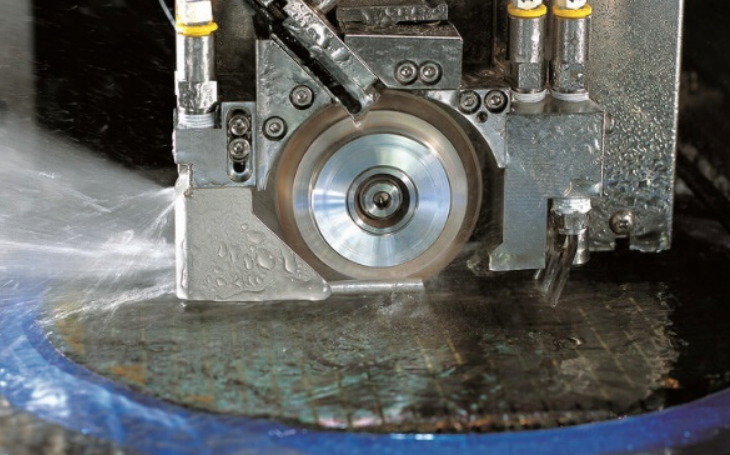
Dengan kemajuan ilmu material, teknologi pemotongan wafer telah berkembang melampaui semikonduktor berbasis silikon tradisional dan mencakup material baru seperti galium nitrida (GaN). Material baru ini, karena kekerasan dan sifat strukturalnya, menimbulkan tantangan baru dalam proses pemotongan, yang membutuhkan penyempurnaan lebih lanjut dalam alat dan teknik pemotongan.
Sebagai proses krusial dalam industri semikonduktor, pemotongan wafer terus dioptimalkan sebagai respons terhadap perkembangan permintaan dan kemajuan teknologi, yang meletakkan dasar bagi teknologi mikroelektronika dan sirkuit terpadu di masa mendatang.
Peningkatan dalam teknologi wafer dicing melampaui pengembangan material dan alat bantu. Peningkatan ini juga mencakup optimasi proses, peningkatan kinerja peralatan, dan kontrol presisi parameter dicing. Kemajuan ini bertujuan untuk memastikan presisi, efisiensi, dan stabilitas tinggi dalam proses wafer dicing, memenuhi kebutuhan industri semikonduktor akan dimensi yang lebih kecil, integrasi yang lebih tinggi, dan struktur chip yang lebih kompleks.
Area Peningkatan | Langkah-langkah Khusus | Efek |
Optimasi Proses | - Meningkatkan persiapan awal, seperti penempatan wafer dan perencanaan jalur yang lebih akurat. | - Mengurangi kesalahan pemotongan dan meningkatkan stabilitas. |
- Meminimalkan kesalahan pemotongan dan meningkatkan stabilitas. | - Mengadopsi mekanisme pemantauan dan umpan balik waktu nyata untuk menyesuaikan tekanan, kecepatan, dan suhu alat. | |
- Menurunkan tingkat kerusakan wafer dan meningkatkan kualitas chip. | ||
Peningkatan Kinerja Peralatan | - Memanfaatkan sistem mekanis presisi tinggi dan teknologi kontrol otomasi canggih. | - Meningkatkan akurasi pemotongan dan mengurangi pemborosan material. |
- Memperkenalkan teknologi pemotongan laser yang cocok untuk wafer material berkekerasan tinggi. | - Meningkatkan efisiensi produksi dan mengurangi kesalahan manual. | |
- Meningkatkan otomatisasi peralatan untuk pemantauan dan penyesuaian otomatis. | ||
Kontrol Parameter yang Tepat | - Sesuaikan secara cermat parameter seperti kedalaman pemotongan, kecepatan, jenis alat, dan metode pendinginan. | - Memastikan integritas cetakan dan kinerja kelistrikan. |
- Sesuaikan parameter berdasarkan bahan wafer, ketebalan, dan struktur. | - Meningkatkan tingkat hasil, mengurangi limbah material, dan menurunkan biaya produksi. | |
Signifikansi Strategis | - Terus mengeksplorasi jalur teknologi baru, mengoptimalkan proses, dan meningkatkan kemampuan peralatan untuk memenuhi permintaan pasar. | - Meningkatkan hasil dan kinerja produksi chip, mendukung pengembangan material baru dan desain chip canggih. |
1.2 Pentingnya Pemotongan Wafer
Pemotongan wafer memainkan peran penting dalam proses manufaktur semikonduktor, yang secara langsung memengaruhi langkah-langkah selanjutnya serta kualitas dan kinerja produk akhir. Kepentingannya dapat dirinci sebagai berikut:
Pertama, akurasi dan konsistensi pemotongan merupakan kunci untuk memastikan hasil dan keandalan chip. Selama proses manufaktur, wafer menjalani beberapa langkah pemrosesan untuk membentuk berbagai struktur sirkuit yang rumit, yang harus dibagi secara presisi menjadi chip-chip individual (die). Jika terdapat kesalahan signifikan dalam penyelarasan atau pemotongan selama proses pemotongan, sirkuit dapat rusak, yang memengaruhi fungsionalitas dan keandalan chip. Oleh karena itu, teknologi pemotongan presisi tinggi tidak hanya memastikan integritas setiap chip tetapi juga mencegah kerusakan pada sirkuit internal, sehingga meningkatkan tingkat hasil keseluruhan.
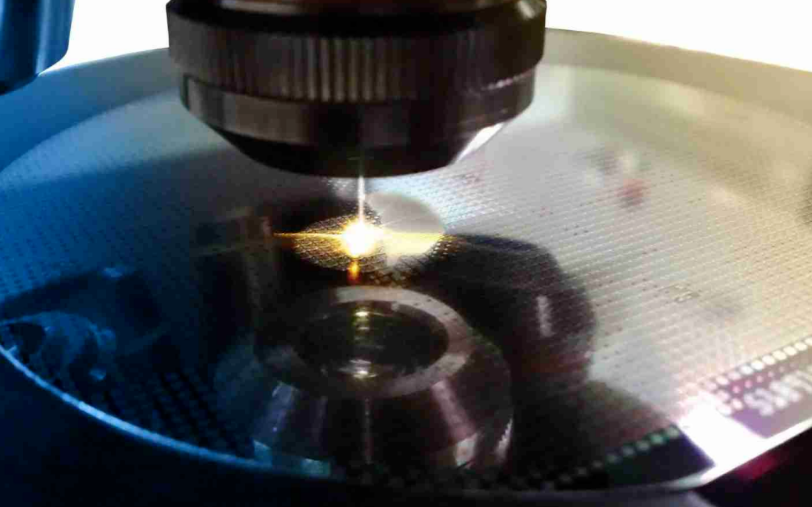
Kedua, pemotongan wafer memiliki dampak signifikan terhadap efisiensi produksi dan pengendalian biaya. Sebagai langkah krusial dalam proses manufaktur, efisiensinya secara langsung memengaruhi kemajuan langkah-langkah selanjutnya. Dengan mengoptimalkan proses pemotongan wafer, meningkatkan tingkat otomatisasi, dan meningkatkan kecepatan pemotongan, efisiensi produksi secara keseluruhan dapat ditingkatkan secara signifikan.
Di sisi lain, pemborosan material selama pemotongan merupakan faktor krusial dalam manajemen biaya. Pemanfaatan teknologi pemotongan canggih tidak hanya mengurangi kehilangan material yang tidak perlu selama proses pemotongan, tetapi juga meningkatkan pemanfaatan wafer, sehingga menurunkan biaya produksi.
Dengan kemajuan teknologi semikonduktor, diameter wafer terus meningkat, dan kepadatan sirkuit pun meningkat, sehingga menuntut teknologi dicing yang lebih tinggi. Wafer yang lebih besar membutuhkan kontrol jalur pemotongan yang lebih presisi, terutama di area sirkuit dengan kepadatan tinggi, di mana deviasi sekecil apa pun dapat menyebabkan beberapa chip rusak. Selain itu, wafer yang lebih besar membutuhkan lebih banyak jalur pemotongan dan langkah proses yang lebih kompleks, sehingga memerlukan peningkatan lebih lanjut dalam presisi, konsistensi, dan efisiensi teknologi dicing untuk memenuhi tantangan ini.
1.3 Proses Pemotongan Wafer
Proses pemotongan wafer mencakup semua tahapan, mulai dari tahap persiapan hingga pemeriksaan kualitas akhir, dengan setiap tahapan sangat penting untuk memastikan kualitas dan kinerja kepingan yang telah dipotong. Berikut penjelasan detail setiap tahapannya.
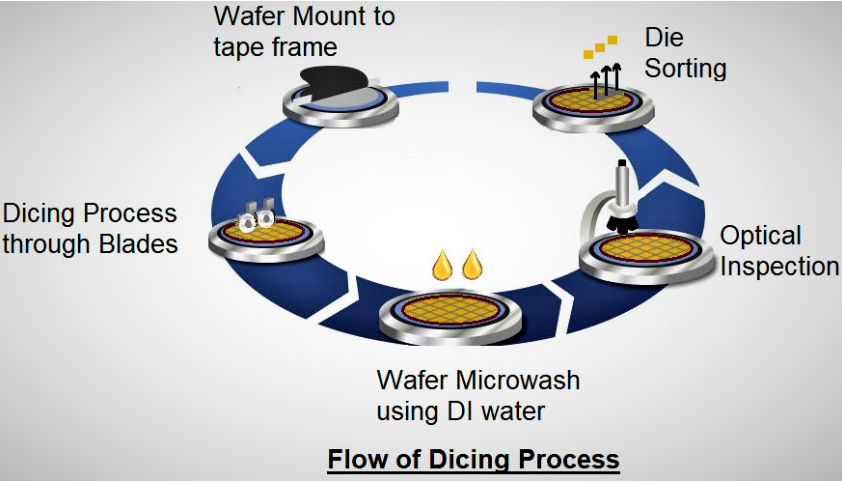
Fase | Deskripsi Rinci |
Tahap Persiapan | -Pembersihan Wafer: Gunakan air dengan kemurnian tinggi dan bahan pembersih khusus, dikombinasikan dengan penggosokan ultrasonik atau mekanis, untuk menghilangkan kotoran, partikel, dan kontaminan, guna memastikan permukaan bersih. -Posisi yang Tepat: Gunakan peralatan presisi tinggi untuk memastikan wafer terbagi secara akurat di sepanjang jalur pemotongan yang dirancang. -Fiksasi Wafer: Amankan wafer ke rangka pita untuk menjaga kestabilan selama pemotongan, mencegah kerusakan akibat getaran atau gerakan. |
Tahap Pemotongan | -Pisau Potong: Menggunakan bilah berlapis berlian yang berputar dengan kecepatan tinggi untuk pemotongan fisik, cocok untuk bahan berbasis silikon dan hemat biaya. -Pemotongan Laser: Memanfaatkan sinar laser berenergi tinggi untuk pemotongan non-kontak, ideal untuk material yang rapuh atau sangat keras seperti galium nitrida, menawarkan presisi yang lebih tinggi dan kehilangan material yang lebih sedikit. -Teknologi Baru: Memperkenalkan teknologi pemotongan laser dan plasma untuk lebih meningkatkan efisiensi dan presisi sekaligus meminimalkan zona yang terkena panas. |
Tahap Pembersihan | - Gunakan air deionisasi (air DI) dan bahan pembersih khusus, dikombinasikan dengan pembersihan ultrasonik atau semprot, untuk menghilangkan serpihan dan debu yang dihasilkan selama pemotongan, mencegah residu memengaruhi proses selanjutnya atau kinerja listrik chip. - Air DI dengan kemurnian tinggi menghindari masuknya kontaminan baru, sehingga menjamin lingkungan wafer yang bersih. |
Tahap Inspeksi | -Inspeksi Optik: Gunakan sistem deteksi optik yang dikombinasikan dengan algoritma AI untuk mengidentifikasi cacat dengan cepat, memastikan tidak ada retakan atau keretakan pada potongan dadu, meningkatkan efisiensi pemeriksaan, dan mengurangi kesalahan manusia. -Pengukuran Dimensi: Verifikasi bahwa dimensi chip memenuhi spesifikasi desain. -Pengujian Kinerja Listrik: Memastikan kinerja kelistrikan chip penting memenuhi standar, menjamin keandalan dalam aplikasi selanjutnya. |
Tahap Penyortiran | - Gunakan lengan robot atau cangkir hisap vakum untuk memisahkan chip yang memenuhi syarat dari rangka pita dan secara otomatis memilahnya berdasarkan kinerja, memastikan efisiensi dan fleksibilitas produksi sekaligus meningkatkan presisi. |
Proses pemotongan wafer meliputi pembersihan, pemosisian, pemotongan, pembersihan, inspeksi, dan penyortiran wafer, dengan setiap langkahnya sangat penting. Dengan kemajuan dalam teknologi otomatisasi, pemotongan laser, dan inspeksi AI, sistem pemotongan wafer modern dapat mencapai presisi, kecepatan, dan kehilangan material yang lebih rendah. Di masa depan, teknologi pemotongan baru seperti laser dan plasma secara bertahap akan menggantikan pemotongan pisau tradisional untuk memenuhi kebutuhan desain chip yang semakin kompleks, yang selanjutnya mendorong perkembangan proses manufaktur semikonduktor.
Teknologi Pemotongan Wafer dan Prinsip-Prinsipnya
Gambar ini mengilustrasikan tiga teknologi pemotongan wafer yang umum:Pisau PotongBahasa Indonesia:Pemotongan Laser, DanPemotongan PlasmaBerikut adalah analisis terperinci dan penjelasan tambahan mengenai ketiga teknik tersebut:
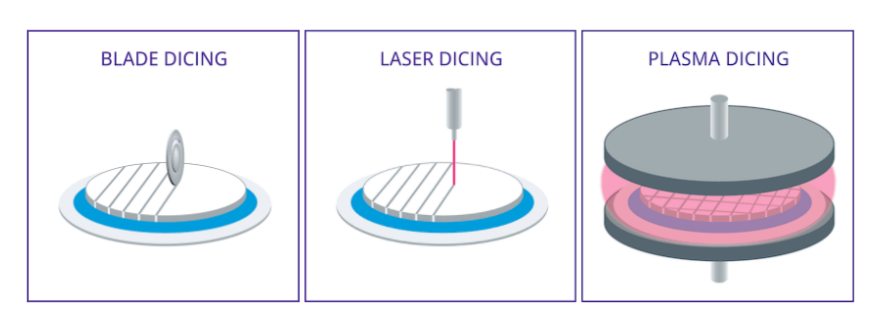
Dalam manufaktur semikonduktor, pemotongan wafer merupakan langkah krusial yang membutuhkan pemilihan metode pemotongan yang tepat berdasarkan ketebalan wafer. Langkah pertama adalah menentukan ketebalan wafer. Jika ketebalan wafer melebihi 100 mikron, pemotongan bilah dapat dipilih sebagai metode pemotongan. Jika pemotongan bilah tidak sesuai, metode pemotongan fraktur dapat digunakan, yang mencakup teknik pemotongan scribe dan pemotongan bilah.
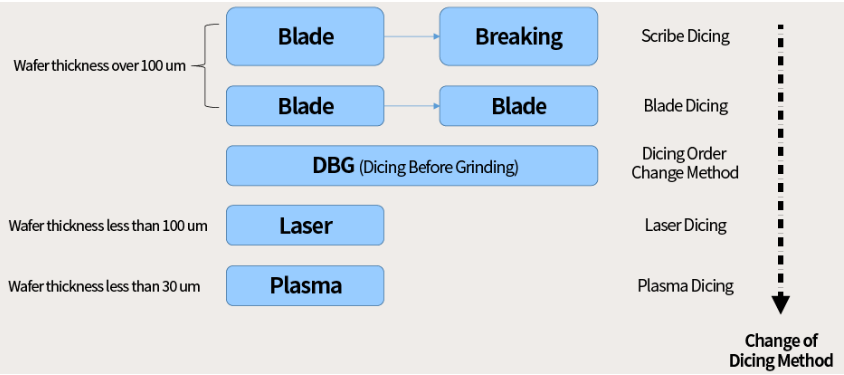
Untuk ketebalan wafer antara 30 dan 100 mikron, metode DBG (Dice Before Grinding) direkomendasikan. Dalam hal ini, pemotongan scriber, pemotongan blade, atau penyesuaian urutan pemotongan sesuai kebutuhan dapat dipilih untuk mencapai hasil terbaik.
Untuk wafer ultra-tipis dengan ketebalan kurang dari 30 mikron, pemotongan laser menjadi metode yang lebih disukai karena kemampuannya memotong wafer tipis secara presisi tanpa menyebabkan kerusakan berlebih. Jika pemotongan laser tidak dapat memenuhi persyaratan tertentu, pemotongan plasma dapat digunakan sebagai alternatif. Diagram alir ini memberikan alur pengambilan keputusan yang jelas untuk memastikan pemilihan teknologi pemotongan wafer yang paling sesuai untuk berbagai kondisi ketebalan.
2.1 Teknologi Pemotongan Mekanis
Teknologi pemotongan mekanis merupakan metode tradisional dalam pemotongan wafer. Prinsip utamanya adalah menggunakan roda gerinda berlian yang berputar berkecepatan tinggi sebagai alat pemotong untuk mengiris wafer. Peralatan utamanya meliputi spindel bantalan udara, yang menggerakkan roda gerinda berlian dengan kecepatan tinggi untuk melakukan pemotongan atau pembuatan alur yang presisi di sepanjang jalur pemotongan yang telah ditentukan. Teknologi ini banyak digunakan dalam industri karena biayanya yang rendah, efisiensinya yang tinggi, dan penerapannya yang luas.
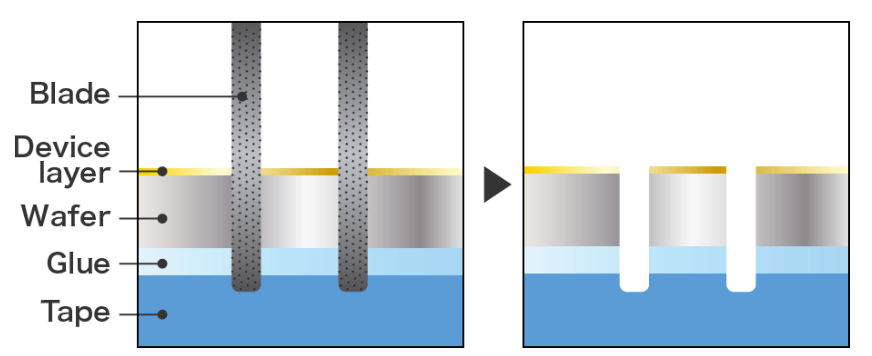
Keuntungan
Kekerasan dan ketahanan aus yang tinggi pada roda gerinda berlian memungkinkan teknologi pemotongan mekanis beradaptasi dengan kebutuhan pemotongan berbagai material wafer, baik material berbasis silikon tradisional maupun semikonduktor majemuk yang lebih baru. Pengoperasiannya sederhana, dengan persyaratan teknis yang relatif rendah, semakin meningkatkan popularitasnya dalam produksi massal. Selain itu, dibandingkan dengan metode pemotongan lain seperti pemotongan laser, pemotongan mekanis memiliki biaya yang lebih terkendali, sehingga cocok untuk kebutuhan produksi bervolume tinggi.
Keterbatasan
Meskipun memiliki banyak keunggulan, teknologi pemotongan mekanis juga memiliki keterbatasan. Pertama, akibat kontak fisik antara alat dan wafer, presisi pemotongan relatif terbatas, yang seringkali menyebabkan deviasi dimensi yang dapat memengaruhi akurasi pengemasan dan pengujian chip selanjutnya. Kedua, cacat seperti terkelupas dan retak dapat dengan mudah terjadi selama proses pemotongan mekanis, yang tidak hanya memengaruhi tingkat rendemen tetapi juga dapat berdampak negatif pada keandalan dan masa pakai chip. Kerusakan akibat tekanan mekanis sangat merugikan untuk manufaktur chip berdensitas tinggi, terutama saat memotong material rapuh, di mana masalah ini lebih menonjol.
Peningkatan Teknologi
Untuk mengatasi keterbatasan ini, para peneliti terus mengoptimalkan proses pemotongan mekanis. Peningkatan utama meliputi penyempurnaan desain dan pemilihan material roda gerinda untuk meningkatkan presisi dan daya tahan pemotongan. Selain itu, optimalisasi desain struktural dan sistem kontrol peralatan pemotongan telah semakin meningkatkan stabilitas dan otomatisasi proses pemotongan. Kemajuan ini mengurangi kesalahan yang disebabkan oleh operasi manusia dan meningkatkan konsistensi pemotongan. Pengenalan teknologi inspeksi dan kendali mutu canggih untuk pemantauan anomali secara real-time selama proses pemotongan juga telah meningkatkan keandalan dan hasil pemotongan secara signifikan.
Pengembangan Masa Depan dan Teknologi Baru
Meskipun teknologi pemotongan mekanis masih memegang peranan penting dalam pemotongan wafer, teknologi pemotongan baru berkembang pesat seiring perkembangan proses semikonduktor. Misalnya, penerapan teknologi pemotongan laser termal memberikan solusi baru untuk masalah presisi dan cacat pada pemotongan mekanis. Metode pemotongan non-kontak ini mengurangi tekanan fisik pada wafer, sehingga secara signifikan mengurangi risiko terkelupas dan retak, terutama saat memotong material yang lebih getas. Di masa mendatang, integrasi teknologi pemotongan mekanis dengan teknik pemotongan yang sedang berkembang akan memberikan lebih banyak pilihan dan fleksibilitas bagi manufaktur semikonduktor, yang selanjutnya meningkatkan efisiensi manufaktur dan kualitas chip.
Kesimpulannya, meskipun teknologi pemotongan mekanis memiliki beberapa kelemahan, perbaikan teknologi yang berkelanjutan dan integrasinya dengan teknik pemotongan baru memungkinkannya untuk tetap memainkan peran penting dalam manufaktur semikonduktor dan mempertahankan daya saingnya dalam proses masa depan.
2.2 Teknologi Pemotongan Laser
Teknologi pemotongan laser, sebagai metode baru dalam pemotongan wafer, secara bertahap mendapatkan perhatian luas di industri semikonduktor karena presisinya yang tinggi, minimnya kerusakan kontak mekanis, dan kemampuan pemotongan yang cepat. Teknologi ini memanfaatkan kepadatan energi dan kemampuan pemfokusan sinar laser yang tinggi untuk menciptakan zona kecil yang terpengaruh panas pada permukaan material wafer. Ketika sinar laser diterapkan pada wafer, tegangan termal yang dihasilkan menyebabkan material tersebut patah di lokasi yang ditentukan, sehingga menghasilkan pemotongan yang presisi.
Keunggulan Teknologi Pemotongan Laser
• Presisi Tinggi: Kemampuan pemosisian sinar laser yang presisi memungkinkan presisi pemotongan tingkat mikron atau bahkan nanometer, memenuhi persyaratan manufaktur sirkuit terpadu modern berpresisi tinggi dan berdensitas tinggi.
• Tidak Ada Kontak Mekanis:Pemotongan laser menghindari kontak fisik dengan wafer, mencegah masalah umum dalam pemotongan mekanis, seperti terkelupas dan retak, secara signifikan meningkatkan tingkat hasil dan keandalan serpihan.
• Kecepatan Pemotongan Cepat: Kecepatan tinggi pemotongan laser berkontribusi pada peningkatan efisiensi produksi, membuatnya sangat cocok untuk skenario produksi berskala besar dan berkecepatan tinggi.
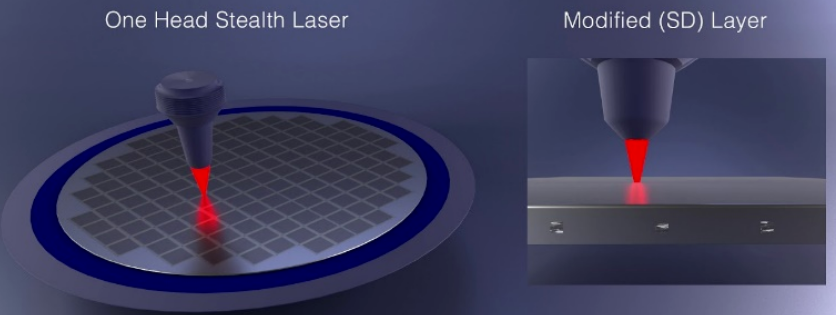
Tantangan yang Dihadapi
• Biaya Peralatan Tinggi:Investasi awal untuk peralatan pemotongan laser tinggi, yang menimbulkan tekanan ekonomi, terutama bagi perusahaan produksi skala kecil hingga menengah.
• Kontrol Proses Kompleks:Pemotongan laser memerlukan kontrol yang tepat terhadap beberapa parameter, termasuk kepadatan energi, posisi fokus, dan kecepatan pemotongan, sehingga membuat prosesnya rumit.
• Masalah Zona Terkena Dampak PanasMeskipun sifat non-kontak pemotongan laser mengurangi kerusakan mekanis, tekanan termal yang disebabkan oleh zona terpengaruh panas (HAZ) dapat berdampak negatif pada sifat material wafer. Optimalisasi proses lebih lanjut diperlukan untuk meminimalkan efek ini.
Arah Peningkatan Teknologi
Untuk mengatasi tantangan ini, para peneliti berfokus pada penurunan biaya peralatan, peningkatan efisiensi pemotongan, dan pengoptimalan aliran proses.
• Laser dan Sistem Optik yang Efisien: Dengan mengembangkan laser yang lebih efisien dan sistem optik yang canggih, biaya peralatan dapat diturunkan sekaligus meningkatkan presisi dan kecepatan pemotongan.
• Mengoptimalkan Parameter Proses:Penelitian mendalam tentang interaksi antara laser dan bahan wafer sedang dilakukan untuk meningkatkan proses yang mengurangi zona yang terkena panas, sehingga meningkatkan kualitas pemotongan.
• Sistem Kontrol Cerdas:Pengembangan teknologi kontrol cerdas bertujuan untuk mengotomatisasi dan mengoptimalkan proses pemotongan laser, meningkatkan stabilitas dan konsistensinya.
Teknologi pemotongan laser sangat efektif dalam wafer ultra-tipis dan skenario pemotongan presisi tinggi. Seiring bertambahnya ukuran wafer dan kepadatan sirkuit, metode pemotongan mekanis tradisional kesulitan memenuhi tuntutan presisi tinggi dan efisiensi tinggi dalam manufaktur semikonduktor modern. Berkat keunggulannya yang unik, pemotongan laser menjadi solusi pilihan di bidang ini.
Meskipun teknologi pemotongan laser masih menghadapi tantangan seperti biaya peralatan yang tinggi dan kompleksitas proses, keunggulan uniknya dalam presisi tinggi dan kerusakan non-kontak menjadikannya arah penting untuk pengembangan manufaktur semikonduktor. Seiring dengan kemajuan teknologi laser dan sistem kontrol cerdas, pemotongan laser diharapkan dapat semakin meningkatkan efisiensi dan kualitas pemotongan wafer, mendorong perkembangan berkelanjutan industri semikonduktor.
2.3 Teknologi Pemotongan Plasma
Teknologi pemotongan plasma, sebagai metode pemotongan wafer yang sedang berkembang, telah mendapatkan perhatian signifikan dalam beberapa tahun terakhir. Teknologi ini menggunakan sinar plasma berenergi tinggi untuk memotong wafer secara presisi dengan mengendalikan energi, kecepatan, dan jalur pemotongan sinar plasma, sehingga mencapai hasil pemotongan yang optimal.
Prinsip Kerja dan Keuntungan
Proses pemotongan plasma bergantung pada sinar plasma bersuhu tinggi dan berenergi tinggi yang dihasilkan oleh peralatan. Sinar ini dapat memanaskan material wafer hingga titik leleh atau penguapannya dalam waktu yang sangat singkat, sehingga memungkinkan pemotongan yang cepat. Dibandingkan dengan pemotongan mekanis atau laser tradisional, pemotongan plasma lebih cepat dan menghasilkan zona yang terpengaruh panas lebih kecil, sehingga secara efektif mengurangi terjadinya retakan dan kerusakan selama pemotongan.
Dalam aplikasi praktis, teknologi pemotongan plasma sangat handal dalam menangani wafer dengan bentuk kompleks. Sinar plasma berenergi tinggi dan dapat disesuaikan dapat dengan mudah memotong wafer dengan bentuk tidak beraturan dengan presisi tinggi. Oleh karena itu, dalam manufaktur mikroelektronika, terutama dalam produksi chip kelas atas yang disesuaikan dan dalam jumlah kecil, teknologi ini menunjukkan potensi besar untuk digunakan secara luas.
Tantangan dan Keterbatasan
Meskipun teknologi pemotongan plasma memiliki banyak keuntungan, teknologi ini juga menghadapi beberapa tantangan.
• Proses Kompleks:Proses pemotongan plasma rumit dan membutuhkan peralatan presisi tinggi dan operator berpengalaman untuk memastikanakurasi dan stabilitas dalam pemotongan.
• Pengendalian dan Keselamatan Lingkungan: Sifat sinar plasma yang bersuhu tinggi dan berenergi tinggi memerlukan pengendalian lingkungan dan langkah-langkah keamanan yang ketat, yang meningkatkan kompleksitas dan biaya penerapan.
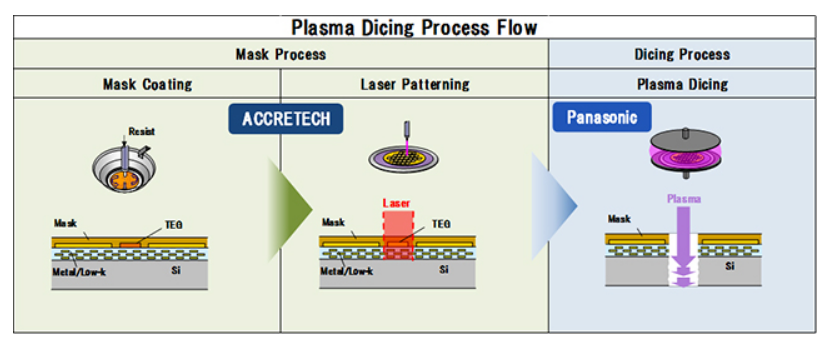
Arah Pengembangan Masa Depan
Dengan kemajuan teknologi, tantangan terkait pemotongan plasma diperkirakan akan teratasi secara bertahap. Dengan mengembangkan peralatan pemotongan yang lebih cerdas dan stabil, ketergantungan pada operasi manual dapat dikurangi, sehingga meningkatkan efisiensi produksi. Di saat yang sama, optimalisasi parameter proses dan lingkungan pemotongan akan membantu mengurangi risiko keselamatan dan biaya operasional.
Dalam industri semikonduktor, inovasi dalam teknologi pemotongan dan pengirisan wafer sangat penting untuk mendorong perkembangan industri. Teknologi pemotongan plasma, dengan presisi tinggi, efisiensi, dan kemampuannya untuk menangani bentuk wafer yang kompleks, telah muncul sebagai pemain baru yang signifikan di bidang ini. Meskipun masih terdapat beberapa tantangan, masalah ini akan diatasi secara bertahap dengan inovasi teknologi yang berkelanjutan, yang akan menghadirkan lebih banyak kemungkinan dan peluang bagi manufaktur semikonduktor.
Prospek penerapan teknologi pemotongan plasma sangat luas, dan diperkirakan akan memainkan peran yang lebih penting dalam manufaktur semikonduktor di masa mendatang. Melalui inovasi dan optimalisasi teknologi yang berkelanjutan, pemotongan plasma tidak hanya akan mengatasi tantangan yang ada, tetapi juga menjadi pendorong utama pertumbuhan industri semikonduktor.
2.4 Kualitas Pemotongan dan Faktor-Faktor yang Mempengaruhi
Kualitas pemotongan wafer sangat penting untuk pengemasan, pengujian, serta kinerja dan keandalan produk akhir secara keseluruhan. Masalah umum yang dihadapi selama pemotongan meliputi retakan, terkelupas, dan penyimpangan pemotongan. Masalah-masalah ini dipengaruhi oleh beberapa faktor yang bekerja sama.
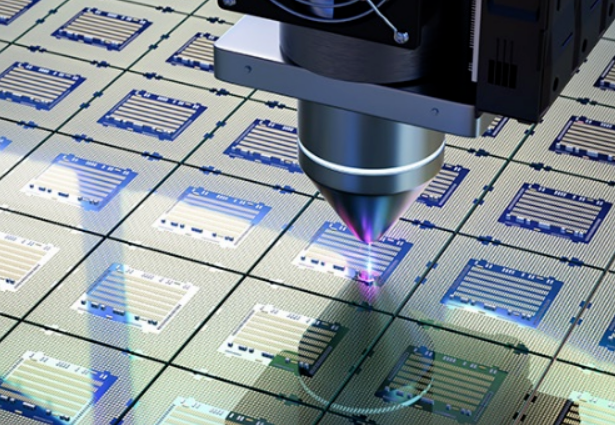
Kategori | Isi | Dampak |
Parameter Proses | Kecepatan potong, laju umpan, dan kedalaman pemotongan secara langsung memengaruhi stabilitas dan presisi proses pemotongan. Pengaturan yang tidak tepat dapat menyebabkan konsentrasi tegangan dan zona terpengaruh panas yang berlebihan, yang mengakibatkan retakan dan pecah. Menyesuaikan parameter secara tepat berdasarkan material wafer, ketebalan, dan kebutuhan pemotongan merupakan kunci untuk mencapai hasil pemotongan yang diinginkan. | Parameter proses yang tepat memastikan pemotongan yang tepat dan mengurangi risiko cacat seperti retak dan pecah. |
Faktor Peralatan dan Material | -Kualitas PisauMaterial, kekerasan, dan ketahanan aus mata pisau memengaruhi kelancaran proses pemotongan dan kerataan permukaan pemotongan. Mata pisau berkualitas buruk meningkatkan gesekan dan tekanan termal, yang berpotensi menyebabkan keretakan atau terkelupas. Memilih material mata pisau yang tepat sangatlah penting. -Kinerja PendinginPendingin membantu menurunkan suhu pemotongan, meminimalkan gesekan, dan membersihkan serpihan. Pendingin yang tidak efektif dapat menyebabkan suhu tinggi dan penumpukan serpihan, yang memengaruhi kualitas dan efisiensi pemotongan. Memilih pendingin yang efisien dan ramah lingkungan sangatlah penting. | Kualitas bilah pisau memengaruhi presisi dan kelancaran pemotongan. Pendingin yang tidak efektif dapat mengakibatkan kualitas dan efisiensi pemotongan yang buruk, sehingga perlu penggunaan pendingin yang optimal. |
Kontrol Proses dan Inspeksi Kualitas | -Kontrol Proses: Pemantauan dan penyesuaian parameter pemotongan utama secara real-time untuk memastikan stabilitas dan konsistensi dalam proses pemotongan. -Inspeksi Kualitas: Pemeriksaan penampilan pasca pemotongan, pengukuran dimensi, dan pengujian kinerja kelistrikan membantu mengidentifikasi dan mengatasi masalah kualitas dengan segera, meningkatkan akurasi dan konsistensi pemotongan. | Kontrol proses dan pemeriksaan kualitas yang tepat membantu memastikan hasil pemotongan yang konsisten dan berkualitas tinggi serta deteksi dini potensi masalah. |

Meningkatkan Kualitas Pemotongan
Peningkatan kualitas pemotongan memerlukan pendekatan komprehensif yang mempertimbangkan parameter proses, pemilihan peralatan dan material, pengendalian proses, dan inspeksi. Dengan terus menyempurnakan teknologi pemotongan dan mengoptimalkan metode proses, presisi dan stabilitas pemotongan wafer dapat ditingkatkan lebih lanjut, sehingga memberikan dukungan teknis yang lebih andal bagi industri manufaktur semikonduktor.
#03 Penanganan dan Pengujian Pasca Pemotongan
3.1 Pembersihan dan Pengeringan
Tahap pembersihan dan pengeringan setelah pemotongan wafer sangat penting untuk memastikan kualitas cip dan kelancaran proses selanjutnya. Selama tahap ini, sangat penting untuk membersihkan serpihan silikon, residu pendingin, dan kontaminan lain yang dihasilkan selama pemotongan secara menyeluruh. Sama pentingnya untuk memastikan cip tidak rusak selama proses pembersihan, dan setelah pengeringan, pastikan tidak ada kelembapan yang tersisa di permukaan cip untuk mencegah masalah seperti korosi atau pelepasan muatan listrik statis.
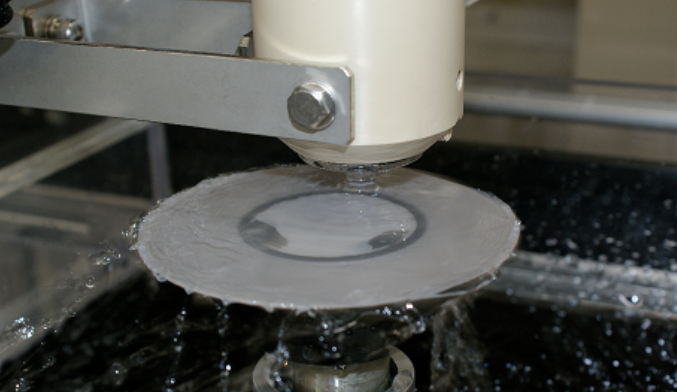
Penanganan Pasca Pemotongan: Proses Pembersihan dan Pengeringan
Langkah Proses | Isi | Dampak |
Proses Pembersihan | -Metode: Gunakan bahan pembersih khusus dan air murni, dikombinasikan dengan teknik penyikatan ultrasonik atau mekanis untuk pembersihan. | Memastikan penghilangan kontaminan secara menyeluruh dan mencegah kerusakan pada chip selama pembersihan. |
-Pemilihan Agen Pembersih: Pilih berdasarkan bahan wafer dan jenis kontaminan untuk memastikan pembersihan yang efektif tanpa merusak chip. | Pemilihan bahan yang tepat merupakan kunci pembersihan dan perlindungan serpihan yang efektif. | |
-Kontrol Parameter: Kontrol secara ketat suhu pembersihan, waktu, dan konsentrasi larutan pembersih untuk mencegah masalah kualitas yang disebabkan oleh pembersihan yang tidak tepat. | Kontrol membantu menghindari kerusakan wafer atau meninggalkan kontaminan, memastikan kualitas yang konsisten. | |
Proses Pengeringan | -Metode Tradisional: Pengeringan udara alami dan pengeringan udara panas, yang memiliki efisiensi rendah dan dapat menyebabkan penumpukan listrik statis. | Dapat menyebabkan waktu pengeringan lebih lambat dan potensi masalah statis. |
-Teknologi Modern: Gunakan teknologi canggih seperti pengeringan vakum dan pengeringan inframerah untuk memastikan keripik cepat kering dan menghindari efek berbahaya. | Proses pengeringan yang lebih cepat dan efisien, mengurangi risiko pelepasan muatan statis atau masalah terkait kelembapan. | |
Pemilihan & Pemeliharaan Peralatan | -Pemilihan Peralatan:Mesin pembersih dan pengering berkinerja tinggi meningkatkan efisiensi pemrosesan dan mengendalikan secara cermat potensi masalah selama penanganan. | Mesin berkualitas tinggi memastikan pemrosesan yang lebih baik dan mengurangi kemungkinan kesalahan selama pembersihan dan pengeringan. |
-Perawatan Peralatan: Pemeriksaan dan pemeliharaan peralatan secara berkala memastikan peralatan tetap dalam kondisi kerja optimal, sehingga menjamin kualitas chip. | Pemeliharaan yang tepat mencegah kegagalan peralatan, memastikan pemrosesan yang andal dan berkualitas tinggi. |
Pembersihan dan Pengeringan Pasca Pemotongan
Tahap pembersihan dan pengeringan setelah pemotongan wafer merupakan proses yang rumit dan rumit yang memerlukan pertimbangan cermat berbagai faktor untuk memastikan hasil akhir yang optimal. Dengan menggunakan metode ilmiah dan prosedur yang ketat, setiap keping dapat dipastikan memasuki tahap pengemasan dan pengujian selanjutnya dalam kondisi optimal.
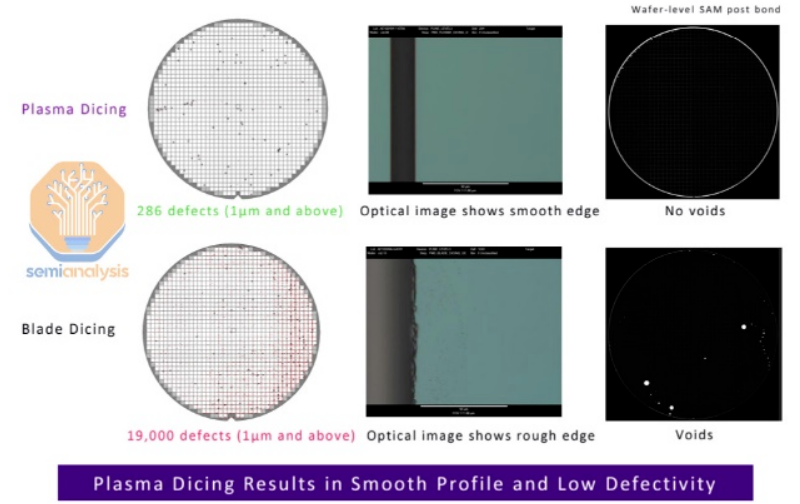
Inspeksi dan Pengujian Pasca Pemotongan
Melangkah | Isi | Dampak |
Langkah Inspeksi | 1.Inspeksi VisualGunakan peralatan inspeksi visual atau otomatis untuk memeriksa cacat yang terlihat seperti retakan, serpihan, atau kontaminasi pada permukaan serpihan. Segera identifikasi serpihan yang rusak secara fisik untuk menghindari pemborosan. | Membantu mengidentifikasi dan menghilangkan serpihan yang rusak sejak dini dalam proses, sehingga mengurangi kehilangan material. |
2.Pengukuran Ukuran: Gunakan perangkat pengukur presisi untuk mengukur dimensi chip secara akurat, memastikan ukuran potongan memenuhi spesifikasi desain dan mencegah masalah kinerja atau kesulitan pengemasan. | Memastikan chip berada dalam batas ukuran yang dibutuhkan, mencegah penurunan kinerja atau masalah perakitan. | |
3.Pengujian Kinerja Listrik: Mengevaluasi parameter kelistrikan utama seperti resistansi, kapasitansi, dan induktansi, untuk mengidentifikasi chip yang tidak sesuai dan memastikan hanya chip yang memenuhi syarat kinerja yang melanjutkan ke tahap berikutnya. | Memastikan hanya chip yang teruji fungsional dan kinerjanya saja yang maju dalam proses, sehingga mengurangi risiko kegagalan di tahap selanjutnya. | |
Langkah Pengujian | 1.Pengujian Fungsional: Memverifikasi bahwa fungsionalitas dasar chip berfungsi sebagaimana mestinya, mengidentifikasi dan menghilangkan chip dengan kelainan fungsional. | Memastikan chip memenuhi persyaratan operasional dasar sebelum melanjutkan ke tahap selanjutnya. |
2.Pengujian Keandalan: Mengevaluasi stabilitas kinerja chip dalam penggunaan jangka panjang atau lingkungan yang keras, biasanya melibatkan penuaan suhu tinggi, pengujian suhu rendah, dan pengujian kelembapan untuk mensimulasikan kondisi ekstrem di dunia nyata. | Memastikan chip dapat berfungsi dengan andal dalam berbagai kondisi lingkungan, meningkatkan umur panjang dan stabilitas produk. | |
3.Pengujian Kompatibilitas: Verifikasi bahwa chip berfungsi dengan baik dengan komponen atau sistem lain, pastikan tidak ada kesalahan atau penurunan kinerja karena ketidakcocokan. | Memastikan pengoperasian yang lancar dalam aplikasi dunia nyata dengan mencegah masalah kompatibilitas. |
3.3 Pengemasan dan Penyimpanan
Setelah pemotongan wafer, cip merupakan hasil penting dari proses manufaktur semikonduktor, dan tahap pengemasan serta penyimpanannya pun sama pentingnya. Langkah-langkah pengemasan dan penyimpanan yang tepat sangat penting, tidak hanya untuk memastikan keamanan dan stabilitas cip selama transportasi dan penyimpanan, tetapi juga untuk memberikan dukungan yang kuat bagi tahap produksi, pengujian, dan pengemasan selanjutnya.
Ringkasan Tahapan Inspeksi dan Pengujian:
Tahapan inspeksi dan pengujian chip setelah pemotongan wafer mencakup berbagai aspek, termasuk inspeksi visual, pengukuran ukuran, pengujian kinerja listrik, pengujian fungsional, pengujian keandalan, dan pengujian kompatibilitas. Tahapan-tahapan ini saling terkait dan saling melengkapi, membentuk fondasi yang kokoh untuk menjamin kualitas dan keandalan produk. Melalui prosedur inspeksi dan pengujian yang ketat, potensi masalah dapat diidentifikasi dan diatasi dengan segera, memastikan produk akhir memenuhi persyaratan dan harapan pelanggan.
Aspek | Isi |
Langkah-langkah Pengemasan | 1.Anti-statis:Bahan pengemasan harus memiliki sifat anti-statis yang sangat baik untuk mencegah listrik statis merusak perangkat atau memengaruhi kinerjanya. |
2.Tahan lembab:Bahan pengemasan harus memiliki ketahanan kelembaban yang baik untuk mencegah korosi dan penurunan kinerja listrik yang disebabkan oleh kelembaban. | |
3.Tahan guncangan:Bahan pengemasan harus menyediakan penyerapan guncangan yang efektif untuk melindungi chip dari getaran dan benturan selama pengangkutan. | |
Lingkungan Penyimpanan | 1.Kontrol Kelembaban: Kontrol kelembapan secara ketat dalam kisaran yang sesuai untuk mencegah penyerapan kelembapan dan korosi yang disebabkan oleh kelembapan yang berlebihan atau masalah statis yang disebabkan oleh kelembapan yang rendah. |
2.Kebersihan: Jaga lingkungan penyimpanan tetap bersih untuk menghindari kontaminasi serpihan oleh debu dan kotoran. | |
3.Kontrol Suhu: Tetapkan rentang suhu yang wajar dan pertahankan kestabilan suhu untuk mencegah penuaan dini akibat panas berlebih atau masalah kondensasi yang disebabkan oleh suhu rendah. | |
Inspeksi Reguler | Periksa dan evaluasi chip yang disimpan secara berkala, menggunakan inspeksi visual, pengukuran ukuran, dan uji kinerja kelistrikan untuk mengidentifikasi dan mengatasi potensi masalah secara tepat waktu. Berdasarkan waktu dan kondisi penyimpanan, rencanakan penggunaan chip untuk memastikannya digunakan dalam kondisi optimal. |
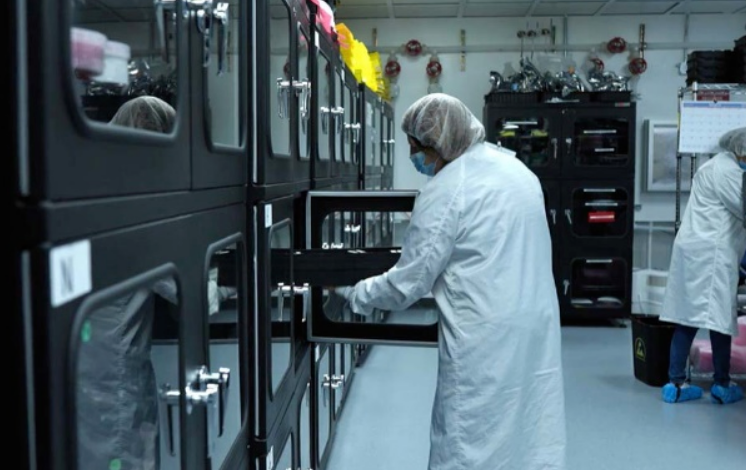
Masalah retakan mikro dan kerusakan selama proses pemotongan wafer merupakan tantangan signifikan dalam manufaktur semikonduktor. Tekanan pemotongan merupakan penyebab utama fenomena ini, karena menciptakan retakan kecil dan kerusakan pada permukaan wafer, yang mengakibatkan peningkatan biaya produksi dan penurunan kualitas produk.
Untuk mengatasi tantangan ini, sangat penting untuk meminimalkan tekanan pemotongan dan menerapkan teknik, alat, dan kondisi pemotongan yang optimal. Perhatian yang cermat terhadap faktor-faktor seperti material bilah, kecepatan pemotongan, tekanan, dan metode pendinginan dapat membantu mengurangi pembentukan retakan mikro dan meningkatkan hasil keseluruhan proses. Selain itu, penelitian yang sedang berlangsung terhadap teknologi pemotongan yang lebih canggih, seperti laser dicing, sedang menjajaki cara-cara untuk lebih memitigasi masalah ini.
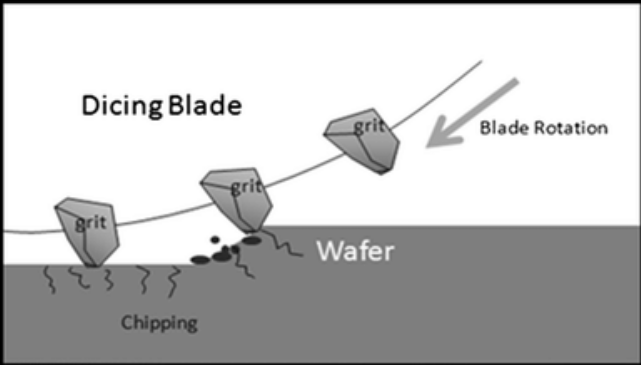
Sebagai material yang rapuh, wafer rentan terhadap perubahan struktur internal ketika mengalami tekanan mekanis, termal, atau kimia, yang menyebabkan terbentuknya retakan mikro. Meskipun retakan ini mungkin tidak langsung terlihat, retakan ini dapat meluas dan menyebabkan kerusakan yang lebih parah seiring berjalannya proses manufaktur. Masalah ini menjadi sangat bermasalah selama tahap pengemasan dan pengujian selanjutnya, di mana fluktuasi suhu dan tekanan mekanis tambahan dapat menyebabkan retakan mikro ini berkembang menjadi fraktur yang terlihat, yang berpotensi menyebabkan kegagalan chip.
Untuk mengurangi risiko ini, penting untuk mengontrol proses pemotongan secara cermat dengan mengoptimalkan parameter seperti kecepatan potong, tekanan, dan suhu. Penggunaan metode pemotongan yang tidak terlalu agresif, seperti laser dicing, dapat mengurangi tekanan mekanis pada wafer dan meminimalkan pembentukan retakan mikro. Selain itu, penerapan metode inspeksi canggih seperti pemindaian inframerah atau pencitraan sinar-X selama proses wafer dicing dapat membantu mendeteksi retakan tahap awal ini sebelum menyebabkan kerusakan lebih lanjut.
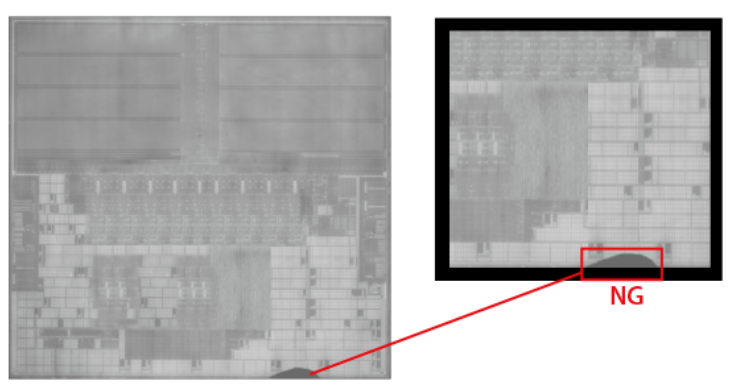
Kerusakan pada permukaan wafer merupakan masalah penting dalam proses pemotongan, karena dapat berdampak langsung pada kinerja dan keandalan chip. Kerusakan tersebut dapat disebabkan oleh penggunaan alat pemotong yang tidak tepat, parameter pemotongan yang salah, atau cacat material yang melekat pada wafer itu sendiri. Apa pun penyebabnya, kerusakan ini dapat menyebabkan perubahan resistansi atau kapasitansi listrik sirkuit, yang memengaruhi kinerja keseluruhan.
Untuk mengatasi masalah ini, dua strategi utama sedang dieksplorasi:
1. Mengoptimalkan alat pemotong dan parameternya: Dengan menggunakan pisau yang lebih tajam, menyesuaikan kecepatan pemotongan, dan memodifikasi kedalaman pemotongan, konsentrasi tegangan selama proses pemotongan dapat diminimalkan, sehingga mengurangi potensi kerusakan.
2. Menjelajahi teknologi pemotongan baruTeknik canggih seperti pemotongan laser dan pemotongan plasma menawarkan presisi yang lebih baik sekaligus berpotensi mengurangi tingkat kerusakan pada wafer. Teknologi ini sedang dipelajari untuk menemukan cara mencapai akurasi pemotongan yang tinggi sekaligus meminimalkan tekanan termal dan mekanis pada wafer.
Area Dampak Termal dan Dampaknya terhadap Kinerja
Dalam proses pemotongan termal seperti pemotongan laser dan plasma, suhu tinggi pasti menciptakan zona dampak termal pada permukaan wafer. Area ini, dengan gradien suhu yang signifikan, dapat mengubah sifat material, sehingga memengaruhi kinerja akhir chip.
Dampak Zona Terkena Dampak Termal (TAZ):
Perubahan Struktur KristalPada suhu tinggi, atom-atom dalam material wafer dapat mengalami penataan ulang, menyebabkan distorsi pada struktur kristal. Distorsi ini melemahkan material, mengurangi kekuatan dan stabilitas mekanisnya, yang meningkatkan risiko kegagalan chip selama penggunaan.
Perubahan Sifat ListrikSuhu tinggi dapat mengubah konsentrasi dan mobilitas pembawa muatan dalam material semikonduktor, sehingga memengaruhi konduktivitas listrik dan efisiensi transmisi arus chip. Perubahan ini dapat menyebabkan penurunan kinerja chip, yang berpotensi membuatnya tidak sesuai dengan tujuannya.
Untuk mengurangi dampak ini, pengendalian suhu selama pemotongan, pengoptimalan parameter pemotongan, dan eksplorasi metode seperti jet pendingin atau perlakuan pasca-pemrosesan merupakan strategi penting guna mengurangi dampak termal dan menjaga keutuhan material.
Secara keseluruhan, retakan mikro dan zona dampak termal merupakan tantangan krusial dalam teknologi pemotongan wafer. Penelitian berkelanjutan, beserta kemajuan teknologi dan langkah-langkah pengendalian mutu, akan diperlukan untuk meningkatkan kualitas produk semikonduktor dan meningkatkan daya saing pasarnya.
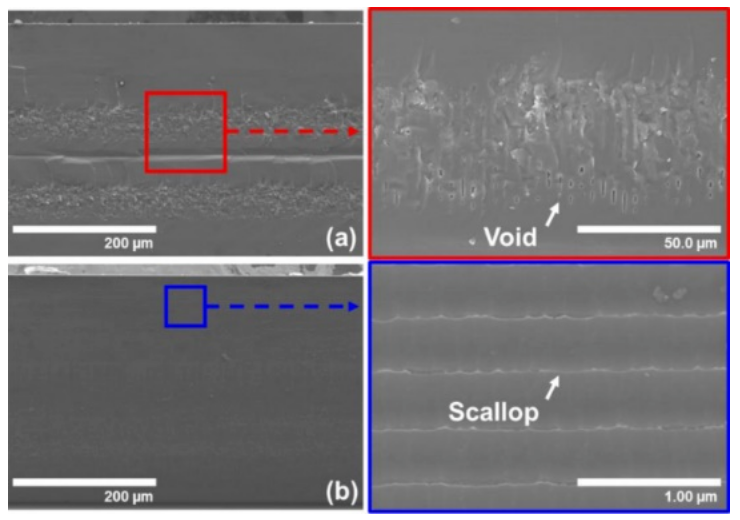
Langkah-langkah Pengendalian Zona Dampak Termal:
Mengoptimalkan Parameter Proses PemotonganMengurangi kecepatan dan daya potong dapat secara efektif meminimalkan ukuran zona dampak termal (TAZ). Hal ini membantu mengendalikan jumlah panas yang dihasilkan selama proses pemotongan, yang secara langsung memengaruhi sifat material wafer.
Teknologi Pendinginan CanggihPenerapan teknologi seperti pendinginan nitrogen cair dan pendinginan mikrofluida dapat secara signifikan membatasi jangkauan zona dampak termal. Metode pendinginan ini membantu menghilangkan panas secara lebih efisien, sehingga mempertahankan sifat material wafer dan meminimalkan kerusakan termal.
Pemilihan MaterialPara peneliti sedang mengeksplorasi material baru, seperti karbon nanotube dan grafena, yang memiliki konduktivitas termal dan kekuatan mekanis yang sangat baik. Material-material ini dapat mengurangi zona dampak termal sekaligus meningkatkan kinerja chip secara keseluruhan.
Singkatnya, meskipun zona dampak termal merupakan konsekuensi tak terelakkan dari teknologi pemotongan termal, zona tersebut dapat dikontrol secara efektif melalui teknik pemrosesan yang dioptimalkan dan pemilihan material. Penelitian di masa mendatang kemungkinan akan berfokus pada penyempurnaan dan otomatisasi proses pemotongan termal untuk mencapai pemotongan wafer yang lebih efisien dan presisi.

Strategi Keseimbangan:
Mencapai keseimbangan optimal antara rendemen wafer dan efisiensi produksi merupakan tantangan berkelanjutan dalam teknologi pemotongan wafer. Produsen perlu mempertimbangkan berbagai faktor, seperti permintaan pasar, biaya produksi, dan kualitas produk, untuk mengembangkan strategi produksi dan parameter proses yang rasional. Di saat yang sama, penerapan peralatan pemotong canggih, peningkatan keterampilan operator, dan peningkatan kontrol kualitas bahan baku sangat penting untuk mempertahankan atau bahkan meningkatkan rendemen sekaligus meningkatkan efisiensi produksi.
Tantangan dan Peluang Masa Depan:
Dengan kemajuan teknologi semikonduktor, pemotongan wafer menghadapi tantangan dan peluang baru. Seiring mengecilnya ukuran chip dan meningkatnya integrasi, tuntutan terhadap presisi dan kualitas pemotongan meningkat secara signifikan. Bersamaan dengan itu, teknologi yang sedang berkembang memberikan ide-ide baru untuk pengembangan teknik pemotongan wafer. Produsen harus selalu mengikuti dinamika pasar dan tren teknologi, terus menyesuaikan dan mengoptimalkan strategi produksi serta parameter proses untuk memenuhi perubahan pasar dan tuntutan teknologi.
Kesimpulannya, dengan mengintegrasikan pertimbangan permintaan pasar, biaya produksi, dan kualitas produk, serta dengan memperkenalkan peralatan dan teknologi canggih, meningkatkan keterampilan operator, dan memperkuat kontrol bahan baku, produsen dapat mencapai keseimbangan terbaik antara hasil wafer dan efisiensi produksi selama pemotongan wafer, yang mengarah pada produksi produk semikonduktor yang efisien dan berkualitas tinggi.
Prospek Masa Depan:
Dengan kemajuan teknologi yang pesat, teknologi semikonduktor berkembang dengan kecepatan yang belum pernah terjadi sebelumnya. Sebagai langkah penting dalam manufaktur semikonduktor, teknologi pemotongan wafer siap untuk perkembangan baru yang menarik. Ke depannya, teknologi pemotongan wafer diharapkan dapat mencapai peningkatan signifikan dalam presisi, efisiensi, dan biaya, yang akan menyuntikkan vitalitas baru bagi pertumbuhan industri semikonduktor yang berkelanjutan.
Meningkatkan Presisi:
Demi mencapai presisi yang lebih tinggi, teknologi pemotongan wafer akan terus mendorong batas-batas proses yang ada. Dengan mempelajari mekanisme fisika dan kimia proses pemotongan secara mendalam dan mengendalikan parameter pemotongan secara presisi, hasil pemotongan yang lebih halus akan tercapai untuk memenuhi persyaratan desain sirkuit yang semakin kompleks. Selain itu, eksplorasi material dan metode pemotongan baru akan meningkatkan hasil dan kualitas secara signifikan.
Meningkatkan Efisiensi:
Peralatan pemotong wafer baru akan berfokus pada desain yang cerdas dan otomatis. Pengenalan sistem kontrol dan algoritma canggih akan memungkinkan peralatan untuk secara otomatis menyesuaikan parameter pemotongan agar sesuai dengan berbagai material dan persyaratan desain, sehingga meningkatkan efisiensi produksi secara signifikan. Inovasi seperti teknologi pemotongan multi-wafer dan sistem penggantian bilah yang cepat akan memainkan peran penting dalam meningkatkan efisiensi.
Mengurangi Biaya:
Mengurangi biaya merupakan arah utama pengembangan teknologi pemotongan wafer. Seiring dengan dikembangkannya material dan metode pemotongan baru, biaya peralatan dan biaya perawatan diharapkan dapat dikontrol secara efektif. Selain itu, optimalisasi proses produksi dan pengurangan tingkat skrap akan semakin mengurangi limbah selama proses manufaktur, yang pada akhirnya akan menurunkan biaya produksi secara keseluruhan.
Manufaktur Cerdas dan IoT:
Integrasi manufaktur pintar dan teknologi Internet of Things (IoT) akan membawa perubahan transformatif pada teknologi pemotongan wafer. Melalui interkonektivitas dan berbagi data antar perangkat, setiap langkah proses produksi dapat dipantau dan dioptimalkan secara real-time. Hal ini tidak hanya meningkatkan efisiensi produksi dan kualitas produk, tetapi juga memberikan perusahaan prediksi pasar dan dukungan pengambilan keputusan yang lebih akurat.
Di masa depan, teknologi pemotongan wafer akan mencapai kemajuan pesat dalam hal presisi, efisiensi, dan biaya. Kemajuan ini akan mendorong perkembangan industri semikonduktor yang berkelanjutan dan menghadirkan lebih banyak inovasi serta kemudahan teknologi bagi masyarakat.
Waktu posting: 19-Nov-2024